Standard costing - the capacity, efficacy, production volume ratios and sales ratios
- Agnes Sopel
- Apr 16, 2023
- 7 min read

Standard costing is driven by labour efficacy, machine utilisation and absorption of overhead. This is called 'lean accounting' but many accountants do not use this technique. It requires tracking variances across costs and it provides good grounds for decision making as it has an impact on increasing sales. We don't spend funds unless it is associated with increasing revenue.
Standard costing is a technique used in management accounting. It involves estimating future sales revenues and costs of products. The total budgeted cost is divided into: direct materials, direct labour, variable overheads and fixed overheads. These budgeted costs are then compared with actual costs. The difference between the standard cost and the actual costs is known as 'variance'. Variances are generally analysed for volume variance and price variances. Significant variances are investigated and remedial actions taken to prevent unwelcome results.
Standard costing is of significant importance in the manufacturing industry where specific products or services are produced repetitively.
Standard costing is an important management planning tool helping managers with controls.
Operation variances
If a standard costing system is to work properly it is important that it is supported by those people who use the information. If people believe that the system does not support them, they will not provide accurate information.
Definitions
There are some important standard costing terms:
Standard - the amount or level set for a performance of a particular activity,
Standard cost - the planned cost for a particular level of activity,
Variance - the different between the standard ( or planned) cost and the actual cost,
Variance analysis - an investigation into and an explanation on why variances occur.
Uses
There are four main uses of standard costing identified:
* Stock valuation - it is the expected or planned price that company will pay for the raw materials. There are difficulties in establishing a standard costs as there are differences if costs for different materials,
* Control - by comparing the actual costs and the standard costs a quick actions can be taken if the costs are not satisfactory,
* Performance measurement - provides information to determine if an organisation is meeting its objectives
* Pricing - it helps businesses to set their selling price.
Application
Standard costing is particularly helpful in those organisations where processes and products are made through repetitive activities. This enables general standard to be set. Standard costing is still used quite widely.
Period
Standard costing should have a short reporting periods so that the actual results can be compared frequently. Corrective actions can be then taken quickly before it is too late. This type of costing may be necessary if market or production conditions frequently change.
Standards
Preparation of standard costs requires great care and attention. Each element of cost is subject to analysis so the initial information needs to be accurate.
Management will need to be informed on the level of activity to be used in preparing of standard costs. The activity level should be chosen that is capable of being achieved. It is possible to choose 'ideal' standard that can only be achieved under inly favourable conditions. But such standard would be unrealistic because ideal conditions rarely prevail. The best standard is the standard that is 'attainable' under favourable conditions, and where allowance is made for losses, wastes and machine downtime. The 'attainable' standard is the one that can be reasonably achieved under realistic working conditions. Some delays and inefficiencies may occur.
There are also 'basic' standard, which are those which remain unchanged for a long period of time. This enables for some consistency to be achieved and allow for some meaningful comparison.
Cost data
There is a considerable cost data required:
* Direct materials: types, quantity and price,
* Direct labour: grades, numbers and rates of pay,
* Variable overheads: the total variable overhead cost broken down into various categories such as employees and support costs,
* Fixed overheads: the total fixed overhead, broken down into various categories such as employee costs, building costs and general administration expenses.
Generally each element comprises of two factors: quantity and price. For example:
* Direct materials (quantity X price),
* Direct labour (hours X hourly rate),
* Fixed overheads (hours X fixed overheads absorption rate),
* Variable overheads (hours X variable overheads absorption rate).
This method is called 'standard absorption costing' and is a commonly used costing strategy.
Standard hours and the absorption of overheads
Standard absorption costing requires overheads to be absorbed on the basis of standard hour. In non-standard costing system it is based on the basis of actual hour. A standard hour represents the amount of work that should be completed within an hour.
Standard time will be calculated as follows:
Number of units X standard hours per unit
It is not calculated by multiplying the number of units by actual hours per unit.
Sales variances
There are number of ways in which sales variances may be calculated. We could deal with planned and actual revenue or sales profit that is more relevant to managers. It involves taking the revenue and deducting the standard cost of sales (not the actual costs). The balance is then compared with the budgeted profits.
Performance measures
Performance measures can be extracted from the standard costing data. It highlights the level of efficacy and spot unfavourable trends to plan for remedial actions.
We can measure the:
* efficacy ratio,
* capacity ratio, and
* production volume ratio.
The three performance measures are presented in the figure below:
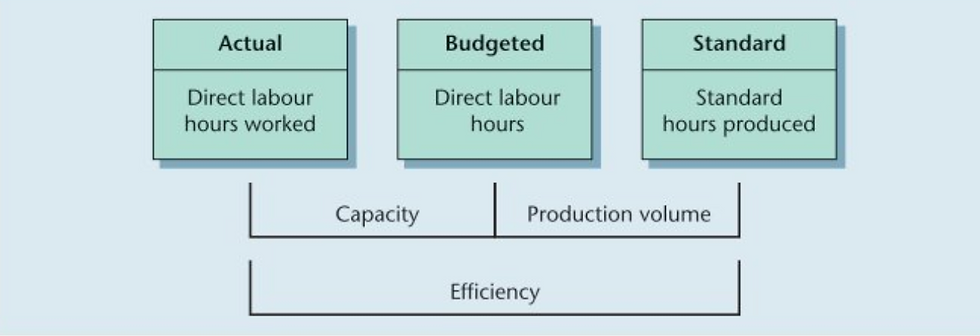
Source: Dyson. J., 2010 "Accounting for non-accounting students', Pearson Prentice Hall
In the table, the 'Actual" hours are those hours actually worked. "Budgeted' hours are those which are planned to be worked and 'Standard' hours measure that actual output produced in standard direct labour hours.
The 'efficacy ratio'
The ratio compares the total 'standard' hours of units produced with the total ' actual' hours taken. The formula is:
(Standard hours produced / Actual direct labour hours worked) X 100
This ratio enables businesses to check on whether the company has produced the units in more or less time then the ones allowed. If the efficacy ratio is over 100% it means that the company has been more efficient with producing the goods then expected.
The 'capacity' ratio
This ratio compares the total actual hours worked with the total budgeted hours. The formula is:
(Actual direct labour hours worked/Budgeted direct labour hours) X 100
This enables management to ascertain whether all the budgeted hours were used to produce actual units. If 100% capacity is not utilised it might be because it was not possible to work the budgeted hours due to not undertaking as much work.
The 'production volume ratio'
This compares the total allowed hours for the work actually produced with the work budgeted hours. The formula is:
(Standard hours produced/ Budgeted direct labour hours) X 100
It enables managers to compare the work produced measured in standard hours with the budgeted hours of work.
Cost variances
The difference between the actual cost and standard cost may result in two main variances: price and quantity. These variances may be (F) favourable to profits, or (A) adverse.
The standard cost variances are presented in figure below:
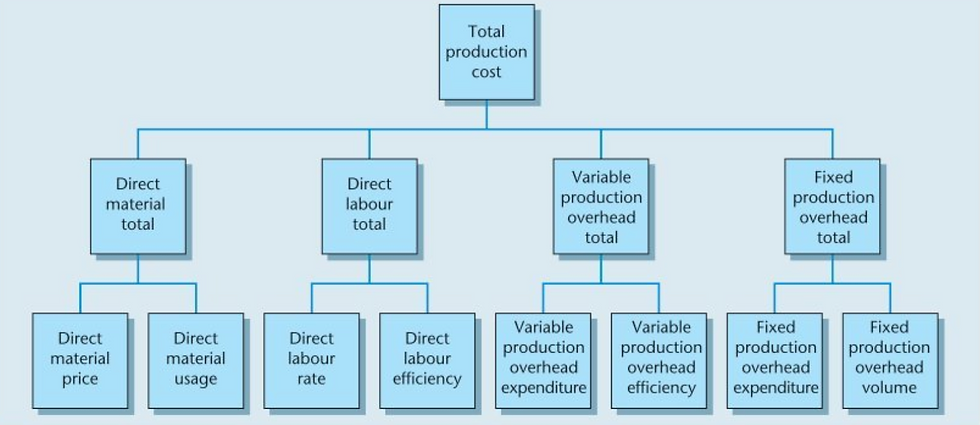
Source: Dyson. J., 2010 "Accounting for non-accounting students', Pearson Prentice Hall
Direct Materials
The Direct materials total would be the ('actual cost per unit' X 'actual quantity used') - ('standard cost per unit' X 'standard quantity used')
The Direct materials price would be the ('actual cost per unit' X 'standard cost per unit') - 'total actual quantity used'
The Direct materials usage would be the ('total actual quantity used' - 'standard quantity for actual production') X standard cost
Direct labour
The Direct labour total would be the ('actual hourly rate' X 'actual hours') - ('standard hourly rate' X ' standard hours')
The Direct labour rate would be the ('actual hourly rate - 'standard hourly rate') X 'actual hours worked'
The Direct labour efficacy would be the ('actual hours worked' - 'standard hours per actual production') X standard hourly rate
Variable production overhead
The Variable production overhead total would be the ('standard hours per actual production' X 'variable production overhead absorption rate')
The Variable production overhead expenditure would be the 'actual variable overhead' - ('actual hours worked' X variable production overhead absorption rate')
The Variable production overhead efficacy would be the ('standard hours per actual production' - 'actual hours worked') X 'variable production overhead absorption rate'
Fixed production overhead
The Fixed production overhead total would be the 'actual fixed overhead - ('standard hour of production' X 'fixed overhead absorption rate')
The Fixed production overhead expenditure would be the 'actual fixed overhead' - 'budgeted fixed expenditure'
The Fixed production overhead volume would be the 'budgeted fixed overhead expenditure' - ('standard hours for actual production' X 'fixed overhead absorption rate')
An example of calculating of operational variances is presented below;

Source: Dyson. J., 2010 "Accounting for non-accounting students', Pearson Prentice Hall

Source: Dyson. J., 2010 "Accounting for non-accounting students', Pearson Prentice Hall

Source: Dyson. J., 2010 "Accounting for non-accounting students', Pearson Prentice Hall

Source: Dyson. J., 2010 "Accounting for non-accounting students', Pearson Prentice Hall

Source: Dyson. J., 2010 "Accounting for non-accounting students', Pearson Prentice Hall
Sales variances
In the absorption costing system the 'sales variance' would be classified into the 'selling price' and the 'sales volume profit variance' as presented in the figure below.

Source: Dyson. J., 2010 "Accounting for non-accounting students', Pearson Prentice Hall
The Total Sales variance would be the ('actual sales revenue' - (actual sales quantity' X 'standard cost per unit') - ('budgeted quantity' X 'standard profit per unit'))
The Selling price variance would be the ('actual sales revenue - ('actual sales quantity' X 'standard cost per unit' ) - ('actual quantity' X 'standard profit per unit'))
Alternatively it can be calculated as the (' actual selling price per unit' - 'standard selling price per unit') X 'actual sales quantity'
The Sales volume profit variance would be the ('actual quantity' - 'budgeted quantity') X 'standard profit per unit'
An example of calculating of sales variances is presented below:

Source: Dyson. J., 2010 "Accounting for non-accounting students', Pearson Prentice Hall

Source: Dyson. J., 2010 "Accounting for non-accounting students', Pearson Prentice Hall
Operating statements
Once all the variances have been calculated they may be summarised in the form of operating statements. Example of such statement is presented in figures below.

Source: Dyson. J., 2010 "Accounting for non-accounting students', Pearson Prentice Hall

Source: Dyson. J., 2010 "Accounting for non-accounting students', Pearson Prentice Hall

Source: Dyson. J., 2010 "Accounting for non-accounting students', Pearson Prentice Hall
The operating profit statements will provide information on whether investigation should be started on the reasons of these variances. Generally the policy would be investigating the variances which are significant, irrespective on whether these are favourable or adverse. Only exceptional variances would be investigated. Business would have a policy of what would be acceptable as exceptional.
Conclusion
It may be difficult to understand for managers how standard costing is being calculated. It is unlikely that as non-accountants we will have to calculate them ourselves. Our job would be mainly to investigate the causes in order to take the necessary actions.
References: Source: Dyson. J., 2010 "Accounting for non-accounting students', Pearson Prentice Hall
Comments