Six Sigma - Part 2 - Define
- Agnes Sopel
- Jan 23, 2022
- 9 min read
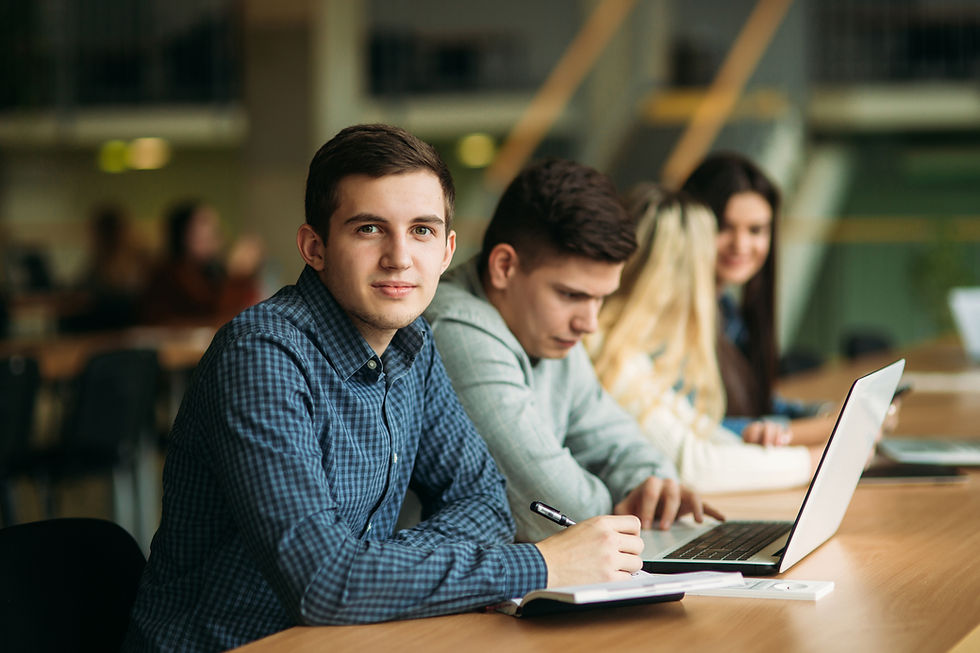
The first step in the Define phase of Six Sigma is to define the project team. These generally consist of the Sponsor, Champion, Project Lead, etc. We also assign responsibilities. After that we gather VOS (Voice of Stakeholders). During this stage we collect input from the stakeholders. After gathering the inputs we try to analyse them and identify them as an improvement needs. From the list of improvement needs we finalise one initiative. In other words, we finalise Lean Six Sigma project. For that project, we make the project charter, which clearly describe the problem, goal, scope, etc. At this point we document the project.
Forming the Project Team
Here, Sponsor, Champion, Project Lead and the Project Mentor should be identified at the beginning of the Define phase.
A Sponsor is a top management executive. Sponsor is responsible for prioritise and finalise the six sigma project. Sponsor also select the lead and champion for the project and actively participates in project discussions. Sponsor initiate the project formally and provide milestone approvals at the end of Define, Measure, Improve and Control Phrase. Sponsor review and approve key decision in Improve phase and provide the necessary leadership support throughout the project.

A Champion is a Senior Manager in the organisation and typically reports to the Sponsor. Usually the Champion is responsible for actively participating in project discussions, review and refine the project charter, closely monitor the progress of the project, review the key deliverables of Define, Measure, Analyse, Improve and Control phases of project, actively participate in key decisions of Improve Phase. The Champion also ensure that the team members are not released from the project till the end and raise corrective actions raised by the project team.
Champion and Sponsor will work closely to resolve any conflicts.
A Project Lead is typically certified a Green Belt or Black Belt. Usually, the Project Lead is responsible for crating and maintaining the project plan and schedule, create and update the project charter, responsible for all the deliverables of Define, Measure, Analyse, Improve and Controls project phases, ensures that all the phases of the project are completed on time, take help of other team members in activities such as data collection, brainstorming sessions, etc. The Project Lead also works with Champion and Sponsor to obtain the milestone approvals at the end of each phase.
A Project Mentor is generally experienced certified Black Belt or Master back Belt individual. Usually, the Project Mentor is responsible for providing Lean Six Sigma Training to the team, review the project charter and the project plan, mentor the team throughout the project life cycle, review the deliverables of Define, Measure, Analyse, Improve and Control phases. The Project Mentor also works with the Sponsor and Champion to highlight any issues and conflicts related to the project. The Project Mentor provides the Sponsor and Champion on Lean Six Sigma methodology and approach.
Gather the Voice of Stakeholders
The Top Management executives provide some inputs into what needs to be improved in the organisation. When we talk to our colleagues in various departments in the organisation some improvement areas for organisation will also come to life. Sometimes we get the improvement areas from various improvement forums, such as weekly status meetings, mostly review meetings etc.Internal surveys we do in the organisation, such as customer satisfaction and employee satisfaction survey also provide some inputs on the areas to improve.

We may engage in External surveys with our customers or other stakeholders to know and identify needs that need to be improved in the organisation, There is another method, called Focus Group Discussions, where we focus on a discussion with one group at a time, for example, we focus on Quality Department and get their input we discuss with the Sales team, then with project managers and so on. We may get some input on improvement areas from Suggestion Box or Idea Box or similar approach in an organisation. When we visit industrial exhibitions and conferences we may observe how our peer organisations are performing that affect the way we need to improve in our organisation. Another source for the input on improvement areas is Competitive comparison. When we go through the formal benchmarking reports we come to know some of the lapses in our business.
Improvement needs
After we have collected various inputs from the stakeholders we need to analyse them and translate them into Improvement needs.
There are two tools: Affinity Diagram and Kano Analysis that help us to translate the stakeholder inputs into the Improvement needs.
Affinity Diagram approach
For example, a Telecom company released a survey to customers.
The feedback was:
- The network should be there even with a tunnel,
- Monthly bill should be on time,
- Want 100 free SMS per month,
- I should get some free local calls per month,
- Internet speed should be good on my mobile,
- I need customer support online (Life chat)
- I need 24/7 customer support on the phone,
- The signal strength should be strong all the time
- Roaming charges should be nil,
- The charges for internet should be low
- I need customer support in my language
- There should be no any hidden charges
In this context affinity means grouping similar concepts into one category.
For example:
Connectivity - network should be there even in a tunnel; the signal strength should be strong all the time
Billing - monthly bill should be on time; there should not be any hidden charges
Free stuff - I should get 100 SMSs free; I should get some free local calls per month; roaming charges should be nil
Internet - internet speed should be good on my mobile; the charges for the internet should be low
Customer support - need customer support online; need customer support in my language; need 24/7 customer support on my phone
Kano analysis
Kano model is a technique to prioritise the improvement needs.
The first set of needs are called: Must Haves. Non-fulfilment of these needs cause dissatisfaction, but cannot increase satisfaction if they are fulfilled. They are also called Basic Needs.
The Next category of needs is called: Delighters, in other words Excitement Needs. If these needs are not fulfilled, it does not cause dissatisfaction but it will delight customers if they are fulfilled.
The next category of needs is called: One-Dimensional needs or Performance needs. The more of these needs that are fulfilled, the more is the satisfaction.
This categorising helps us to prioritise and put more focus on addressing the performance and the basic needs first.

Kano Analysis helps us identify those need that are more prioritised. First the Basic and Performance needs should be addressed. Only then the Delighters should be considered. It would not bring any benefit if we fulfilled only delimiters nd do not address the Basic and Performance needs.
SIPOC
SIPOC ( Supplier, Input, Process, Output, Customer) is a graphical tool to highlight the area of improvement Using SIPOC approach we start at the high level process and go on expanding the selected process at each level, till we reach the desired area of improvement.
We start from the High Level Process, then we mention the inputs for that process, than we capture the supplier, who supply these inputs, and the Output for that process. Finally, we define the Customers who receive the output. As the next step, we expand the High Level Process to the next level sub-process, than we expand the desired sub-process into the next level process and so on.

Finally, we highlight the chosen improvement area.
Select Sig Sigma Project
First and foremost, the project should be strongly aligned with organisational objectives, such as Increase in Revenues, Profits, Customer satisfaction, Employee Satisfaction, etc. The scope of the improvement should be manageable in such a way that the project can complete in 2 months, or 3 months or a maximum of 6 months. The bigger the scope of the project, the higher the complexity and lower the chances of successful completion. If the root causes or solutions are very obvious there is no need for Six sigma effort. Frequently repetitive processes, such as various operational or transactional processes are good candidates for Lean Six Sigma projects.
Once we finalise the Six Sigma project, we proceed to make the project charter.
There is no need to apply all those tools and techniques, just a couple techniques may be needed for a given project. For example, Input from senior management, Focus group discussions and Affinity diagram may be sufficient for one project. For another, input from internal surveys, competitive comparisons and Kano analysis may be sufficient.
Project Charter
Project charter is a document which clearly describes of all the details of a Lean Six Sigma Project.
The Project Charter has following components:
- Problem Statement
- Goal Statement
- Scope of the project
- Business Case for the project
- Project Milestones
- Team structure.
Problem statement
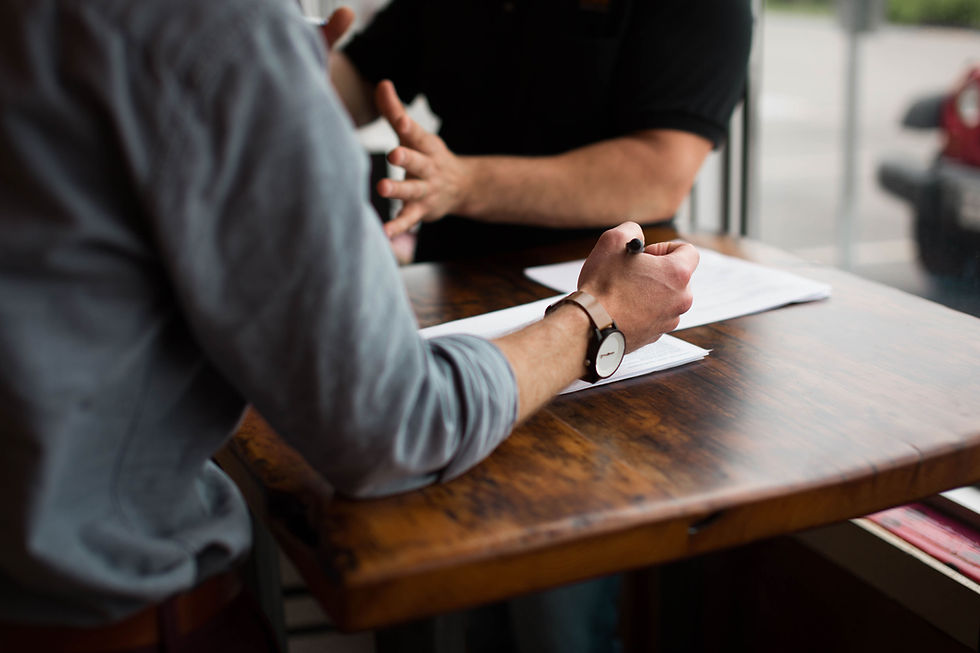
Problem statement is the first component of a project charter. The problem statement should describe what is wrong or what is not satisfactory. It should have a clear description of a problem or concern. The issue that is mentioned in a problem statement, should be a verifiable and measurable fact. It should not be a quest or assumption.
The problem statement, should clearly state on when and where the problem is happening. This ads more clarity to the problem. The problem should also be quantified, indicating the magnitude of the problem. A brief description of the impact and the consequences of the problem should be mentioned in the problem statement.
It is important to be aware of some of the mistakes we usually make when preparing the problem statement. For example, we should not mention the root cause of the problem. We should avoid indicating the assumed solution in the problem statement. The Problem statement should focus only on the problem. The real root causes are identified in Analyse phase. The real solutions to the problem are identified in Improve phase.
Goal Statement

The Goal Statement should specify the exact measurable parameters of the improvement area. This measurable parameter is called the CTQ (Critical to quality). For example, :Improve billing accuracy", "Reduce procurement cycle time" etc. The Goal Statement should specify the quantity and the extend of an improvement. In other words the target for improvement. For example: "Improve billing accuracy to 95%", "Reduce procurement cycle time to 12 days", etc. The goal statement should mention the target timeline for the improvement. For example: "Improve billing accuracy to 95% by the end of this financial year", "Reduce procurement cycle time to 12 days by end of March". This makes the goal statement complete. In short, the goal should be SMART (Specific, Measurable, Achievable, Realistic, Time-bound).
It is important to be aware of some of the mistakes, that we usually make while writing the goal statement. We should not mention or assume the root cause or solution in a goal statement. Such mistakes will make the goal statement biased. Goal statement should focus only on the goal. The real root causes are identified in Analyse phase, and the real solutions to the problem are identified in Improve phase. The goal statement talks only about the goal. Assumed root causes or solutions are not mixed up in the statement. The goal is clearly quantified

It is very important to have a strong alignment in the problem and the goal statements. In there words, problem and goal statements should refer to the came CTQ (Critical to Quality). There should be no mismatch in the problem and the goal statements. If the problem tasks about the delay, we do not make the defect reduction as a goal.
Scope
After Problem and the Goal Statements the next comes the Scope of the project. In the Scope statement, we need to specify what is in scope and what is not in scope of the project. In the "In Scope" section of scope we need to mention the process and functional areas that are is scope of the project. For example: "Only the purchase order process is in scope of this project", "Only the Asia customer segment is in scope of this improvement".
In the "Out of scope" section of project scope we need to mention those processes and functional areas that are out of scope of the project. For example: "The invoice processes are not in scope", "USA, Europe and Australia customer segments are not in scope.
We need to ensure that the scope of the Lean Six Sigma project is manageable. If the scope is huge, the complexity increases and the project might not succeed.
Business Case
The next component of the Project Charter is the Business Case. A Business Case is an executive summary or a small write up on the improvement initiative addressing the following points:
- What are the benefits of doing this project?
- How is the project aligned with the vision and goals of the organisation?
- Why is this project worth doing now?
- What happens if we don't take up this project now?

Milestones of a project
The next component of a Project Charter is Milestones. We need to mention the plan or estimated dates of DMAIC phases of Lean Six Sigma project.
We need to write down the Start and End of each phase: Define, Measure, Analyse, Improve, Control.
Team Structure
The last component of Project Charter is the Team Structure of a project. We need to mention the names of Project Lead, Team Members (if any), Champion, Sponsor and the Project Mentor.
Comments