Six Sigma - Part 1 - Introduction
- Agnes Sopel
- Jan 22, 2022
- 4 min read

We cannot define Six Sigma in just one line. Some people say that it is a metric, others find it as a process improvement method or continuous improvement technique. Many also call it a problem solving tool, business excellence approach or even a statistical analysis toolset.
Metrics
Sometimes people say "my process operates at 1 Sigma level", or our operation is at "3 Sigma levels" or even "6 Sigma Level".
Lets say that we want to measure the order fulfilment process at a restaurant, where the need of a customer is expected to be ready in 15 minutes. Let's assume that there are 200 orders in a day, that equals around 6000 orders per month.
If in a month, there is 4150 orders delayed - 30.85% than the process it at "1 Sigma level".
To move from 1 Sigma Level to 3 Sigma Level, we need to cut the delayed orders to 400 delayed in a month - 93.32%.
To move from 3 Sigma level to 6 Sigma level, we can afford only 1 delayed order in 4 years = 99.9997%.
That is a scale of improvement that Six Sigma Process has to demonstrate.
In another example, we want to measure the payment processing efficacy in an e-commerce company. The expectation is that all payments should be processed successfully. Lets assume that there are 400 payments done a day, which equals 12,000 per month.
If 8298 payments failed in a month, then the process efficacy will be at 1 Sigma level.
To move from 1 Sigma level to 3 Sigma level, we need to cut the number of failed payments to 802 in a month = 93.32%.
To move from 3 Sigma to 6 Sigma level, we can afford only 1 failed payment in 24 months - 99.9997%.
The below table shows all the sigma levels, which is measured by Defects per Million Opportunities or Parts per Million. Both Represent the sale measure.

It requires a lot of effort to move between the Six Sigma Levels of Efficacy.
So the question is, whether by adopting Six Sigma we need to achieve six Sigma Level of 99,9997%?
The answer is: No. All the processes need not aim for 6 Sigma levels. Usually, Mission critical processes need to achieve higher levels.
Six Sigma is a continuous improvement methodology. It is an improvement technique to drive business excellence. It is a set of proven quality tools package in DMAIC ( Define, Measure, Analyse, Improve and Control). It is a structured problem solving method. It is a powerful analytical approach that uses statistics. Six Sigma can also be used as a change management tool. It is not a certification or a standard for organisation. There is no centralised regulatory body, so there is no standard body that awards certification. Instead, certifications, such as Green Belt, Black Belt, are only for individuals.
Six Sigma was originated in Motorola labs in 1970s. In 1980s it was further developed and adopted in automotive industry. During 1990s it was spread to non-manufacturing or service organisations, such as banking, insurance, IT, finance an so on. In 2000s it is widespread across many industries and businesses.
Lean Six Sigma
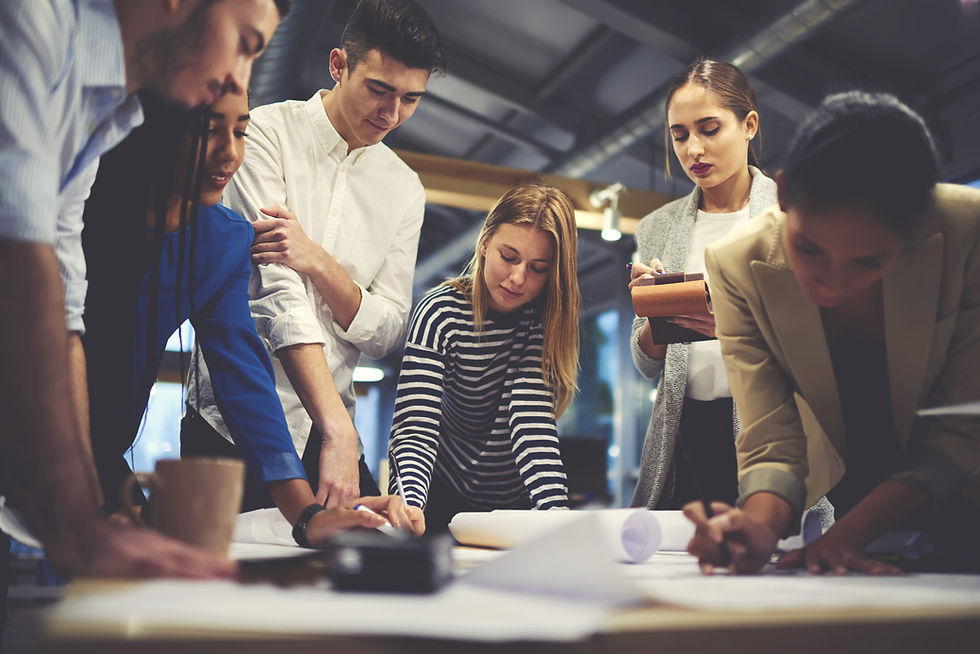
Lean management focuses on identifying and reducing waste in process. Through Lean approach we can make the processes more efficient and lean by eliminating non-value added activities. Lean approach looks at process optimisation only. Unlike Six Sigma Lean does not use the statistical data techniques.
Lean Six Sigma is an integration of Lean management into the Six Sigma methodology of DMAIC. It gives both the strength of Six Sigma and Lean. It is a combination of strong analytical tools of Six-Sigma and in-depth process analysis of Lean.
Benefits for Organisations
By taking up Lean Six Sigma initiatives in organisation we can bring breakthrough improvements. We can reduce costs, defects, cycle time. We can also improve productivity in organisation. Processes can become more predictable, consistent and efficient. We will see improvement in process measurement rigorous as well.
The individual certifications such as Green Belt and Black Belt will help us to grow our career. Lean Six Sigma skillsets will bring improvements in our problem solving and analytical abilities. Our knowledge in process measurements will be improved using various metric, tools and techniques.
21st century demands innovation and creative thinking from us. We can apply Six Sigma to bring improvements in any department such as finance, administration, human resources, training department, production, operations, recruitment, purchasing, sales, marketing and IT infrastructure.
To drive improvements in processes and business, Lean Six Sigma can be applied in any industry, such as: Information Technology, Business Process Outsourcing, Manufacturing, Banking and Finance, Infrastructure, Hospitality, Pharma, Insurance, Healthcare, Airlines, Agriculture, Marketing, Automotive, Real estate, Fashion, Retail, Telecom, Government, Education, Travel & Tourism, Media, Energy and so on.
Examples of improvement projects are:
- Improve on time payments from customers,
- Improve customer satisfaction of ABC service,
- Improve training effectiveness,
- Reduce testing cycle time,
- Reduce defects in product design,
- Reduce recruitment cycle time,
- Improve payroll accuracy,
- Reduce power consumption costs,
- Improve job satisfaction of project teams,
- Reduce delays in project completion,
- Reduce defects in sales proposals,
- Reduce cycle time for customer complaints resolution,
- Improve on time delivery of goods,
- Reduce procurement cycle time,
- Improve accuracy of cost estimation for big size projects.

There is no clash between Six Sigma and other Quality Models. They compliment each other. The other quality models, such as ISO establish the processes and standards across the organisation with certification. With Six Sigma we improve one process at the time and we do not implement lean six sigma to one entire organisation at once. We run multiple Lean Six Sigma initiatives to improve various processes. So it would be not correct to say that an entire organisation would perform at 3 Sigma level. We say, for example, that our Invoicing process perform at 3 Six Sigma Level, or our procurement process is at 2 Sigma Level and so on.
Other Quality Models specify WHAT improvements need to be demonstrated by organisation, whereas the Six Sigma specifies the HOW part, which is the approach by which the desired improvements we will bring.
Comments