Project Management - Types of Projects, Project Life Cycle, Costs, Estimating
- Agnes Sopel
- Mar 20, 2022
- 28 min read

When doing a project, we are stepping into an unknown, there are risks and uncertainty. No two projects can be exactly the same. Projects often exceed their cost, complete late or even being abandoned.
Project management allows to plan, organise and control people and activities, money and tasks so that the projects can be completed successfully. The aim of the project manager is to satisfy the project investors, and all of the stakeholders. That means finishing the project on time, within budget and desired quality.
Types of Projects
There are different types of projects.
For example civil engineering, construction, petrochemical, mining. Those spring most readily to mind whenever industrial projects are mentioned. One common feature, is that the physical work is generally conducted on site from contractors head office. They are often open to public eye and not often pleasing to the view. They come with specific risks and problems. They might require massive capital investment and they need rigorous management of the process, time, finance, and quality.
Operations are generally hazardous to health and safety, particularly in construction, tunnelling and mining. The organisation and communications are likely to be rather complicated, by participation by many different specialists and contractors.
The second types of projects are manufacturing projects. They generally result in a piece of electrical or electronic equipment, machine, vehicle or some other products. The finished-product might be purpose built for a specific customer. Also internal research and development projects fall into this category. Manufacturing project often happens in a laboratory, factory or other home-based environment. More difficult in this case of a complex product that is developed and manufactured by different companies, sometimes with members based in different countries. Such projects are prone to risks and difficulties in control and coordination arising through organisational complexity, competitors, contacts, long distance communication, multiple languages and conflicting technical standards.
The next type of projects are IT projects associated with management of business change. This class of projects proves the point that every company, can expect a need for project management. These are the projects that arise when companies relocate, develop new computer system, launch a marketing campaign, prepare for trade exhibition, produce a study report, restructure the organisation. Not all projects are constructed for profits or other benefits.
Management change projects do not generally result often depends on the successful outcome and they require enormous investment. There were several cases, where failure to implement computer system correctly, has caused a serious operational breakdown.
There are also projects for pure scientific research. These are truly a special case. They may result in dramatically profitable discoveries, but also consume a vast amounts of money or many years without any economical benefits. These research projects carry the highest risks, because they attempt to extend the boundaries of current human knowledge. Often it is impossible to define the projects objectives. These do not generally fall into project management structure, but some level of control is still required. Money and other resources, cannot be spend recklessly.
A sensible method of controlling scientific research is to conduct regular management reviews and reassessment of potential value of the project. The reviews cannot be too often as they will become a burdensome. A decision can be taken at any review to stop the project or release new funding.
Project Life Cycles
Some projects come into being gradually or slowly fade away, so that their beginning and the end dates can be difficult to recognise. Most projects, however should have determined start and the end date. The period between the beginning and the end of a project is usually referred as to the project life cycle. Generally the 3 key players in the project life cycle are: the customer, contractor and the project manager.
These definitions do not apply strictly to all projects, but often adequate to many projects at the high level. Sometimes the customer and the contractor are within the same company.
Small Projects
Small projects generally have short durations. They also generally do not require a significant investments and are straightforward to manage.

As presented in the graph, true projects start and finish with the customer. The cycle reviews number of steps. This is, however, a very simplistic view of the project life cycle, as we do not see the death or disposal of the product, process or project. But this simple holds good for small, simple projects. Most capital projects have many more phases that can usually be identified.
More comprehensive projects
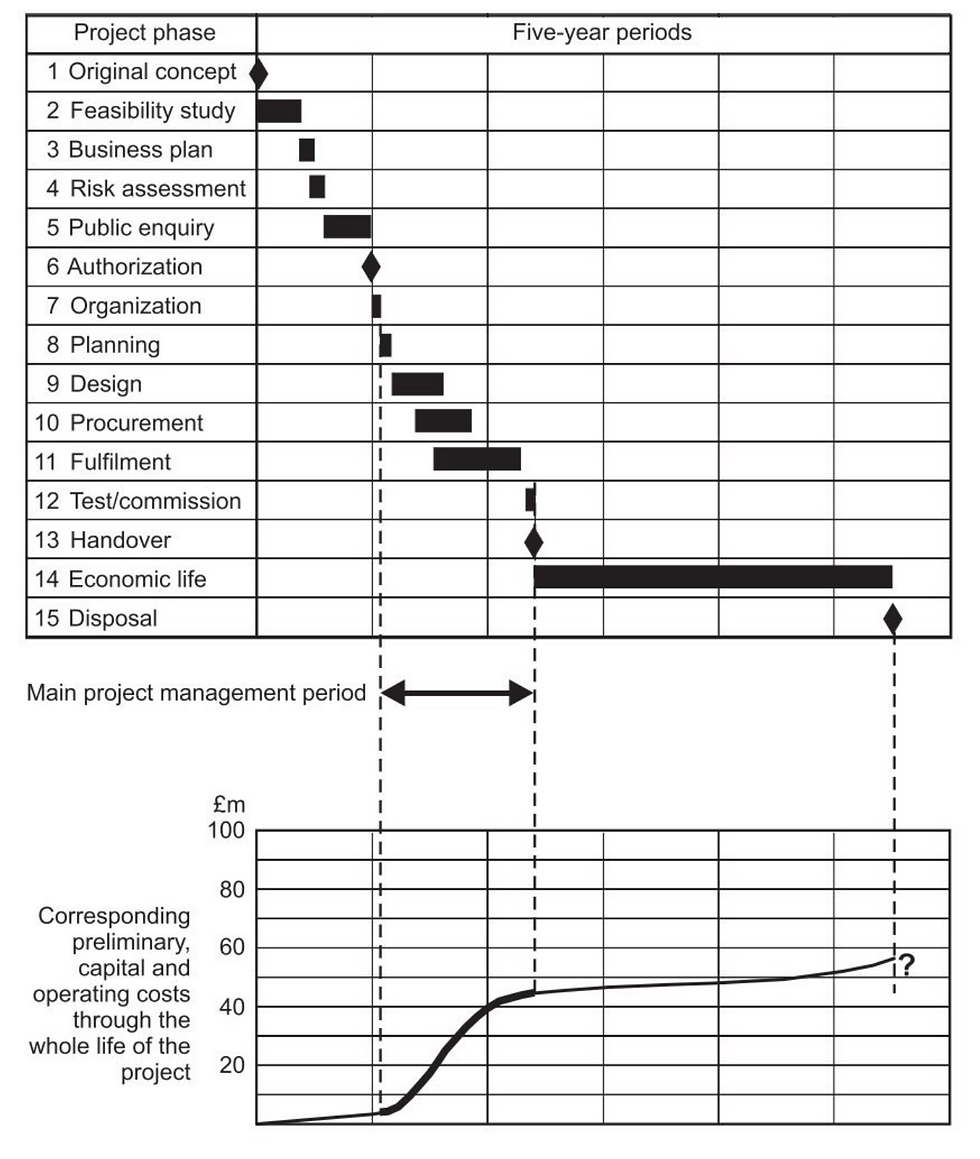
As presented in the figure above the six phases in a small project life cycle, can turn into 15 separate stages. Projects differ, however, and one size cannot always fit all.
The figure above is a gantt chart setting out stages of large capital project. As you can see the project span here is over 27.5 years.
All projects begin as a concept. Someone in the business recognise a need for a project. Phase 1 to 4 are the formative period, which should end in a proposal and a business plan that describes the project, sets out financial requirements, the intended benefits and the principal milestones. Projects in a public eye or which have significant potential environmental or social impact might have to be subjected to one or more public enquiries and prolonged planning applications - Phase 5. This can seriously delay or prevent the actual project.
Once everyone agreed the project definition, funds are available, the project can be authorised in Phase 6. Authorisation should really be only an event of milestone, rather than a time consuming phase. Some organisations, however, are very cautious about this process and can sometimes drag this for several months. This to release resources and make funds available.
When the project has been authorised the organisation has to be put in place. This is the Phase 7 and 6 on our graph. Phase 7 includes the appointment of a project manager and setting of an office space and other accommodation. Then, the real project can start. Phase 8 therefore involves all the planning and mobilisation of the workforce.
Phase 9, 10 and 11 cover the period of design, procurement and manufacture or construction. The project is finished when it is handed over to the customer to be put into operation. But this cannot usually be done before the contractor has performed relevant tests and trials.
The figure above also shows that the version of the project life history begins much ealier, but also does finish until very much later, when the outcome of the project has come to an end and even has been scrapped.
The graph in the lower portion of the figure above sets out the pattern of expenditure that might be expected throughout the project life cycle. Some expenditure must be made by the project owner or sponsor during the formative definition phase. In the example the expenditure is at the modest level. However, some projects require considerate investigation before they can even start. A feasibility study costing sometimes million of pounds, to explore risks, benefits and the best strategy for the proposed project.
The portion of the expenditure curve drawn in the bold line relates to the fulfilment period ( Phase 11) when the project management is actively involved. Almost all the money built during this time, should be built into the real project, so that it adds value as well as costs. Expenditure usually build up very slowly as people are gradually assigned work on the project, with only few staff involved at the early stages to carry out initial design and planning. Later as drawings and specifications begin to emerge from the designer to the technologists, money has to be committed to buying materials so that the workforce can engage to use the purchases to fulfil the project. Nearer the end of the fulfilment phase most purchasing costs are over, and people begin to leave the project. This expenditure is typical of almost all projects and its commonly known as S-curve. It is the time when project manager has most influence over control of capital costs and the progress.
Phase 14 marks the end of the expenditure on the project capital costs and the project moves into a completely different mode. This is the useful operating time of the project, when all the expenditure involved is operating, maintenance, repairs and consumable materials. This is the period when building can remain occupied, an IT system remains efficient, a special machine continue to perform or produces minerals at an economic rate.
When the project nears at the end of economic life, wither the owner has no further use for it, or the costs of operating, maintenance and repair begin to raise to uneconomic proportions. So the time comes to dispose of the project.
Customers, Clients, Contractors and End Users
Customer is the person or organisation for which the project is being conducted. We can also use the "project owner" or "client" in this context. The project customer is traditionally a person or organisation that pay another organisation money in return for a project. In many change management projects the company is, in effect, the customer and contractor, with the board of the senior management of the company acting as the customer whilst the manager or department instructed to carry out the project assumes the role of contractor.
Contractor is the organisation that is principally responsible for executing the project work to the customer requirements. We are not restricting this term to its more common use. It is any organisation or group that carries out the project, whether or not the project is carried out against a formal sales contract.
End user is the individual or organisation that will ultimately own or operate the project. This is not always the same person or organisation that paid for the original project. The original project customer may sell the project on to one or more end users.
Success of Failure?
The manager of a typical project would consider the project successful if it finished on time, to the desired quality and within the budgeted costs. These 3 objectives: time, performance and cost, are the traditional parameters to measure the project success or failure. However, other people might have different idea about the project success. A customer who cannot see the expected return on investment might consider the project as a failure. And, the project can only be completely successful if it satisfies all stakeholders.
During definition and planning
Initial project definition leads to a business case on which the decision to authorise the project will start. This definition takes place during Phase 1 to 6. This is clearly too early to measure the failure or success of a products, but it is the time when the foundation of the success of failure are laid.
The failure can also come from:
- the scope being not clear or not understood
- the technical requirements are vague
- estimates of costs, times and operations are too optimistic
- risk assessments are incomplete or flawed
- the intended project strategy is inappropriate
- insufficient provision of funds and cashflow
- interests and concerns of stakeholders are not taken into account
- undue regard is paid to the motivation and behaviour of the people who will execute the project
- insufficient thought is give on how the managers and workpeople affected by the project will adapt to the changes expected of them
- approval to proceed with the project is given for political, personal or intuitive reason without due consideration to the business plan

During execution
When the authorisation has been given for the project to start, the contractor and project manager takes the responsibility for the success of failure. The contractor may be the manager responsible for managing the change or IT department. The success here will depend on the project time, budget and quality (performance). Many things need to be in place and many actions taken during the project execution to help achieving the success. These include:
- good project definition and sound business case
- appropriate choice of project strategy
- strong support of the project from higher management
- availability of sufficient funds and other resources
- business control of change process and authorisation of projects
- technical competence
- strong quality culture throughout the organisation
- suitable organisation structure
- appropriate regard for the health and safety of everyone connected with the project
- good project communications
- well motivated staff
- quick and fair resolution of conflicts
The primary objectives of cost, performance and time are clear. The project manager needs to understand what each of the objectives implies and how they interrelate to each other.
The Cost
Every project should be controlled against specific cost budgets to ensure that expenditure is not exceeded. Failure to complete work within budget will decrease profits and the return on the capital invested. Most projects are undertaken with the expectation of benefits, either on completion or later in the live history. Sometimes, however, there are projects with no initial profit motive. These are for example the pure scientific research programs, projects carried by charities, local and national government projects that are paid for from public funds or other non-profit-sector works.
Even if there is no profit motive strict attention to cost budgets and financial management is vital. A project might be abandoned if funds run our before completion.
The Quality
Quality has often been used as an alternative name for the performance project objective. Perceived quality will depend on the nature of the project:
- performance must at least equal to the specification,
- reliability and freedom from malfunctions
- long useful and economic life
- safe, posing no threat to anyone or anything
- low operating and maintenance costs
- comfort and pleasant impact on human senses
- environmentally friendly
Development projects for consumer goods must produce articles that satisfy market requirements and conform to relevant legislation. The result is a product that is safe, reliable and appealing to a customer. IT system for example, must perform as expected and the accommodation and all other conditions must be conductive to staff satisfaction and productivity.
At one time the responsibility of product performance in manufacturing environments was placed on quality department, where great reliance was placed on inspection and testing to discover faults (non-conformances) and than arranging for the faults to be rectified. In recent years companies embrace the concept of Total Quality Management, where the quality culture is created throughout the organisation with quality built into all design processes. Quality is shared by management from top to bottom.
The Time
Actual progress has to meet or beat planned progress. All significant stages of the project must finish no later than their scheduled dates. Late completion of the project will not please the customer. Continuously falling to meet deadlines will damage the reputation. Any project which continues to use resources beyond the planned finish date can have a knock on effect and disrupt other projects. Very long delays can be caused by procrastination, legal or planning difficulties, shortage of information, lack of funds etc.
The job of the project manager is to achieve success in all areas of the project: time, quality and cost. The are also interrelated. Sometimes a decision needs to be made to giving priority to one of them.
Identifying stakeholders
The range and nature of stakeholders will vary depending on the project. There will be primary stakeholders, for example, project contractor and project owner.
Subcontractors, suppliers, staff are stakeholders too. There are also others who depend on secondary stakeholders.
Once the stakeholders have been identified, a matrix can be used (see figure below).
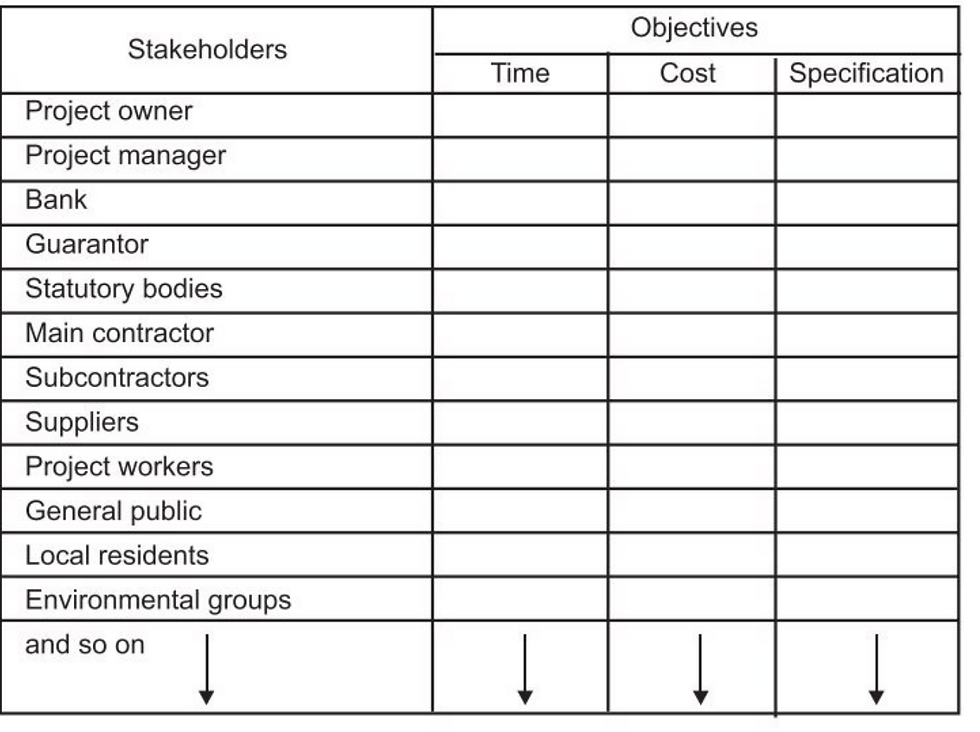
This extends the concept of the triangle of objectives and allows the perceived priorities of all project stakeholders to be considered.
Defining the project
Before any person or organisation decides to start any project, the project requirements must be clearly established, documented and understood. Project objectives can be agreed early in the project stages.
Below figure presents a definition of a large project.

Poor project definition can be very difficult for a contractor. Customers generally are more likely to sign a contract against a fixed price quotations. This is, however, putting contracts at risk. They can have an elegant solution for this. They can identify and list separately all parts of the project that cannot be defined and beyond the contractor control. They can be listed in the tender separately and outside the scope of work. These are known as Provisional cost items. Fixed proposals might be conditional upon no defects are found when the work starts. The provisional cost might be estimated to be charged to he customer should additional work be necessary.
Checklists for new projects can be a very useful way to ensure that an important task or cost is not forgotten. Every enquiry must be registered and given a reference number to be uniquely identified. Than, each enquiry must be evaluated. We need to assess every new enquiry and decide on how to respond. Some enquiries may reveal poorly payment history or an enquiry outside the capacity of the contractor. Sometime screening and approval needs to be established by seiner manager before committing to any work.
Initial enquiries from customers may take different forms. Sometimes these are sets of specifications and drawings, or even written objectives. All of these elements should be suitably documented as "customer specification". It should also be identifiable at all times with relevant reference number, date, issue or revision number.
The Project Scope, Requirements, Specification
Customer specification of a project must be satisfied in every aspect. The contract rules might specify rules of invoicing or even specification of claims of work done. There even might be a penalty specified in the contract, for example, if the dates are not met.
The customer specification should set up all the requirements in unambiguous terms so that they can be understood and interpreted both by the customers and contractors.
Before preparing a proposal the contractor must develop and record the intended strategy nd preliminary investigation. It might be a design drawing or action plan. This must be established before any cost estimating must be done. The golden rule is to define and document the project in all essential respects before estimates are made and translated into budgets and price.
Given the importance in documenting project requirements as accurately as possible it is appropriate to think about correct documentation. In some engineering projects pre-project solution exists called "solution engineering". Sometimes, however, the actual specification might be quite different. Drafts will undertake additions and amendments. It might be re-wised and re0issued several times. There might be piles of drawings, schedules and flowsheets.
A fundamental requirement when a contract is signed is to be able to refer without ambiguity to the correct version of the project specification. Each document should have relevant reference number, serial or label with a version number each time the document is re-issued.
Each specification should contain:
Binder - the specification reserves protection
Specification identifier - the binder should carry specification serial (identification) number, the project number and the project title. All of these should be prominently displayed.
Control schedule of specification documents - revision status of the documentation. It should list every document, also those which cannot be added to the binder and are too large or external. Each document should have its serial number, title and correct revision number. If any of the documents could be very complex, they should have their own schedule.
Descriptive text - narrative describing the project should be written clearly and precisely. The text should be logical and divided into sections.
Supportive documents - those are documents which cannot be added to the binder.
Distribution list - the list of all people who received the initial issue of the specification to ensure relevant changes are suitably communicated.
Estimating Project Costs
Reliable cost estimates are required for all projects. A typical cost summary is presented in figure below.

Let's look at some definitions.
Absorption costing - a method that attempts to recover incorrect costs (overheads) by apportioning them over all the company's direct costs.
Below-the-line-costs - a collective name for various allowances that are added once a total cost estimates are being made. They typically include the allowances for cost escalation, exchange rate fluctuations, contingencies and provisional cost items.
Cost escalation - increases in all costs above their original estimates owing to national cost inflation and increases in wages and salaries. Usually expressed as a rate % per annum if only significant in time for high inflation or for projects planned to last for several years.
Direct costs - costs that can be directly attributed to project work.These are also variable costs, because their rate of expenditure depends on the intensity of project activity. When no work is being done on a project, there is no direct costs.
Cost of sales - equivalent to the sum of all the above the line costs shown in figure above.
General and administrative costs - a general cost burden added as a proportion percent to the above the line costs by some companies to recover selling and other expenses (for instance head office costs) that are nor included in the overhead costs.
Indirect costs - costs that must be incurred by the organisation to provide heat, light, accommodation, insurance, maintenance, accountants, secretaries, welfare, management salaries and other general running costs of the business that cannot be attributed as costs to be changed to a specific project. These are fixed costs as they do not ary from day-to-day. They are also commonly known as overhead costs.
Labour burden - an amount, usually a percentage of wages and salaries that is added to a basic weekly or hourly rate for employee to allow for non-working time and various additional expenses such as the cost of paid holidays, amounts paid by employer as employee benefits, either voluntarily or as a requirement of the national legislation. In the UK, this would include National Insurance contributions. For project estimating and cost control it is convenient if this burden is included in the standard labour costs rates.
Materials burden - an amount added by some contractors to the actual costs of bought out materials to recover their purchasing administration costs.This might be changed 10% or less for very high cost, but 25% on small low-cost items that have relatively high handling and administration costs. A common all around rate used for the materials burden is 15%.
Overhead rate - more properly called the overhead absorption rate, it is a rate calculated by accountants that expresses the company total expected overhead costs for a given period (usually a year) as a proportion of expected direct costs over the same period. It is used to calculate the overhead recovery amount included in prices. There are differences in companies treating overhead costs, but a common method is to apportion the overhead costs as a percentage of direct labour costs. Overhead rates vary considerably from one company to another, perhaps from as low as 50% to 200%. Sometimes contractors will apply different overhead rates to different projects. The rates used will depend on many factors: a ration of direct to indirect staff, the amount of internally funded research and development being done, local authority and public utility charges. High overhead rates, increase price and reduce competitive advantage.
Prime cost - the sum of all direct costs needed to fulfil a particular job or project (direct labour + direct material + direct expenses).
Standard costing - an important and common accounting system in which cost estimates and actual project expenditure are calculated using 'average' or 'standard costs' for direct labour and materials. These standards are calculated by cost accountants as expected averages for each grade of labour and for materials that are commonly held in general stock. Standard costs for materials are particularly relevant to manufacturing projects. Standard labour costs are important for most projects as they greatly simplify the cost estimating and cost accounting. From time to time the accountants check the current standard labour cost against actual expenditure and they will issue revised standard rates whenever the variance become significant (usually the result of cost inflation).
Variance - a term commonly used by accountants to describe difference between actual costs and a standard costs in a standard costing system. More widely, it is the amount by which any actual cost differs from the corresponding estimate to budget. Also used less commonly for the difference in time between the actual event and its planned time. Variances concentrate management attention on departures from budget or plans.
Direct and Indirect costs
There are differences between companies in their interpretation of direct and indirect costs. For example some customers would consider of cost of printing drawings as direct, and other first would treat these costs as indirect and charge them to overheads. It will depend on what customer will agree to pay in the contract and how the price is structured. Cost estimators and project managers must be clear between the distinction of direct and indirect costs, or any exceptions to rules agreed.
Estimating must generally start from the task list. The better the project is defined the less changes on estimating mistakes. However, the possibility of error can never be reduced to zero. Estimates always involves an element of personal judgement and not accurate science. Projects are new ventures and generally contain some costs and risks. Some true costs might sometimes now be known until the end of the project. It is unrealistic to label early estimates as "accurate" or "inaccurate" as there is always uncertainty. steps can, of course, be taken to remove some sources of estimating errors. Cost estimators should be aware of the problems and use data to produce the best estimate possible. Good estimates are essential for effective cost budgets and resource schedules.
Some companies find it convention to classify their projects cost estimates according to the degree of confidence that their estimators can express in their accuracy. This will depend on the quality of information available and the time allowed to prepare the estimates.
Ballpark estimates are those made when only vague information exists and all the details of the work have not been yet decided. These are often also made in emergencies, when detail information are available but someone senior might need a cost estimates in a great hurry. Ballpark estimates are widely used, they are valuable for checks on resources requirements and other early decisions. They are unlikely to provide sufficient accuracy. A good one can achieve -/+ 25% accuracy given a good judgement.
Comparative estimates are made by comparing work to be done on a new project with similar work in the past. They can be attempted before detailed design work take place, when they are no reliable material lists or work schedules. They depend on good project definition, where principal project elements can be identified and accuracy will depend on the degree of confidence. Sometimes it might be possible to achieve -/+15% accuracy. Comparative estimates are often used as the basis for tenders for manufacturing and engineering projects. The estimators might need to built as many contingencies as possible, however.
Feasibility estimates can be derived only after a significant amount of preliminary project design has been carried out. In construction projects, for example, the building specification, site data, provisional layouts and drawings for services are all necessary. Quotations must be obtained from potential suppliers of expensive project equipments or subcontractors and material take-offs and other schedules should be available to use when estimating the costs of materials. The accuracy (confidence factor) should be better than -/+ 10%.
Definitive estimates cannot be made until most design work has been finished, all significant purchase orders have been placed at known prices and work on the project is well in advance and near the completion. Definite estimates can be produced from scratch, but the best practice is to arrive at them by updating the original comparative or feasibility estimates routinely as part of the project cost reporting and control procedure. Barring shocks or distresses during the project execution, the accuracy of the total project estimate should improve as work proceeds and the estimates costs are, one by one, replaced by their actual costs. Estimates can be labelled as definitive when its accuracy is regarded as +/-5% or better. Unless the accounting and cost control systems are flawed, the figures for actual project costs and the definite project estimate should coverage when all work on the project is finished.
The degree of accuracy quotes in these examples are about as good as could ever be expected. It is likely that many organisations will assign wider limits.
All those using estimates for pricing decisions, setting targets, budgets, financial planning or any purpose need to be aware on how much confidence can be placed on the figures put before them. If the organisations estimating procedures recognise and define different categories, such as ballpark, comparative, feasibility, definitive or whatever, than managers can make their decisions accordingly and to better effect.
Estimating for pricing and profits
It is difficult to lay down rules on the degree of estimating accuracy needed for setting fixed prices. Different companies will have their own rules or traditions. For pricing purposes much depends on the size on the intended profit margin, because big margin will cushion the effects of estimating errors. Margins, vary greatly, depending on market conditions and particularly on accepted practise in relevant industry. Reliable estimates are valuable assets for managers faced with difficult task or trying to price a project in an environment of tight competition, where there is no scope for luxury of safety factors such as high mark up on costs or the inclusion of substantial contingency allowances.
The vulnerability of profits to erosion from costs which exceed their budgets is not always appreciated.
Planned profits can fall victims to many risks. Some of them can e predicted. The aim must be to reduce the number of unknown variables or risks as far as possible, and provide sensible allowance to cover those that remain.
Profits deserve protection of goods estimates and budgets. Managing a project which has been underestimated can be a destroying experience, with everything running late.
Estimating capabilities of people
Project cost estimating is never an exact science. When estimating labour times it has to rely on the subjective judgement. The person collecting the project cost estimates needs to be aware that some people will estimate low or some high.
Any estimates can be overstated and understated. May people often feel quite optimistic when estimating time to complete tasks. With such optimistic people we often see the work completed in double or triple the time. More over, some are persistently unable to learn from their previous experience. Therefore, a typical multiplication factor is 1.5, in other words we add at least 50%.
Making allowances, therefore is the best point of action.
Top-Down Estimating
If the project can be divided into few major parts at an early stage, it should be possible to distribute the total estimate over those parts, remembering to leave something in reserve as a separate contingency item. This is called top-bottom estimating. It has the disadvantage, however, of not being based on the detailed project specification, so their accuracy cannot be high.
Bottom-Up Estimating
This is the extreme opposite of the top-down approach. This method can only be used when a good project specification exists and fairly complete task list has been compiled. Bottom-up estimating begins at the lowest level of detail, and it is gradually extended up through the hierarchical structure of the project until the total estimated project cost is reached. These are generally made our later in the project life-cycle history, when it is more known about the project.
At the first stage of the bottom-up cost estimating process it is to compile list of every known item that is going to cost money. This can be difficult, but any left item can the cost to be underestimated.
Each task selected should be small enough to be visualised easily for estimating purposes. On the other hand, the task must be large enough to represent measurable significant part of the whole project.
Careful consideration of all significant tasks will allow for better cost estimating, budgeting, scheduling and subsequent control.
Preparation of Work Breakdown Structure complete with cost is a logical way of considering any project for cost estimating.
Every company with sufficient experience can also develop estimating checklists. A full checklist would include all necessary factors - technical, commercial, statutory, environmental, social and so on. Projects might also consist of number of soft tasks, for example in software development projects). Preparation of schedules, testing.
Very often there are also forgotten tasks. For example, in manufacturing projects, these can be painting, heat treatment, inspection and testing.
Sometimes contracts require project contractors to provide training facilities for some of the customer's staff. New systems implementation often require considerable staff training as well as preparing training manuals beforehand.
Estimating formats
Project cost estimates contain a large amount of data. This data should be presented in a format that will allow easy future reference. Estimates should be tabulated according to a standard company procedure itemised where possible by cost codes in WBS. Can can ensure easy comparisons later. This is an essential part of the cost control function.
All estimating forms are spreadsheets. A large project will need many of these. The WBS is the ideal way to achieve this.

Each item should have a cost code allocated according to hierarchical system. These codes are essential for database sorting and retrieval, not only for estimates, but also for their corresponding costs. This allows for any item to be estimated.
General purpose estimating format
Below design can be used on many kind of projects in Microsoft Excel. It allows for six labour grades to be shown and assumes that all hours will be costed at standard cost rates. Six grades should be adequate, provided that the standard costing system has been designed sensibly and not complicated. The standard grade code and cost rate used should be entered in the space at the head of each column to show the rates used at the time of estimating.
The inclusion of the column headed "longest lead time" in the materials section might appear unusual, however, the people who estimate material costs usually are the same people who can predict delivery times. It is efficient to collect both these sets of data as early as possible an on the same occasion. This extends the usefulness of the estimating into valuable information for timescale planning.

The general-purpose project can also use bellow summarised cost estimates format assisting in pricing. The form allows the figures and formula used in the cost/pricing relationship to be recorded but does not restrict the pricing mechanism too rigidly.

Large project format
In large projects, general purpose forms are inadequate for listing all the cost estimate considerations for purchases materials, components and materials. For example, for construction projects. Below format can be used for listing the cost estimates of significant items of equipment and other high-cost purchases required for the project. Provisions are used on this form to include freight and duty costs which are relevant when the delivery site is instanced.
Totals of convenient subtotals from materials and other materials schedules can be transferred to this type of form to allow the complete project materials costs to be summarised and totalled.

Estimating manufacturing costs
Manufacturing organisations prefer to use drawings, part lists or bills of materials as the basis for making cost estimates. Those documents allow accurate estimation of the raw materials and components needed, and production engineers can work out the operations needed to make the parts and estimate the labour times from those. Several common key factors can be identified in the use of routine methods. Work is always broken down into small elements before estimates are applied. The estimates themselves can usually be described as "standard" or "known" quantities and any need for guesswork is either eliminated or reduced to a minimum. Reliance is put not on personal opinions on how long the job should take, but on the results of long experience (sometimes supported by detailed analysis and even scientific work measurement).
Project work estimating is usually quite different from routine manufacturing estimating, because the estimates must be made long before detailed drawings exists. Often, detailed design yet still to take place and manufacturing drawings do not yet exist. The only information on which a cost estimate can be based is an engineers written design specification. This specification includes little or no information about dimensions, materials. It might state functional performance expected of a completed product. Standard estimating tables will be no help here, as there might be no drawings from which to break the work down into its operations and there might be no hope for using standard estimates. Drawings and part lists are the customary means and without these we are unwilling to forecast. In such situations the estimating process might proceed along the following lines.
First, a description of the product is needed with some idea of the product content. The design engineers will be able to provide the information. Once the description of the product is made it is usually possible to scan archives to find previous piece of work which bears some resemblance to the new job. Classification and coding of past work can be a great help when making such search. It might be found, that no direct comparison exists, but a previous job similar found was a little simpler. we might determine within the engineer that it was 10% simpler and 10% more components would be used. When the materials estimate is done the production manager might be able to estimate the operational costs, given the estimate of 10% increase in materials. He might find that two-week job might therefore increase to two and half week job. In these man-weeks and man-hours are general choices. This way the cost estimates can be set in a broad ways at the early stages.
Estimating Project labour costs
Standard costs make the life of the cost estimator relatively easy, because there is no need to consider differences in wages and salaries paid to different people. The cost estimator cannot possibly name the individuals who will be performing the job. The wages and salaries can be kept confidential.
The first step is to determine standard labour costs rates to classify people according to some convenient rules. Categories which companies generally find suitable are listed below:
Grade 1 - company directors, divisional managers, professional staff, consultants
Grade 2 - department managers, chief engineers of specialist engineering groups
Grade 3 - project engineers and senior engineers
Grade 4 - engineers
Grade 5 - drawings office and checkers
Grade 6 - draughtsmen and women, clerical administrative staff except managers
The number of grades should be kept to a minimum - no more than 10. The accountants work out the average salary costs for those in each grade. All estimates and actual job are costed using these grades and standard rates.
Because the standards are worked out within accountants departments, the methods have an advantage to present confidentiality of individuals earnings; the cost estimators need only be told the standard rate.
Generally speaking, because the labour rates change from year to year, the time to catty out a particular job by a given method should not. Work-time is therefore regarded as the fundamental basis for labour cost estimates. Conversion from work-hours to money can only be regarded as secondary process which is dependent on the costs changes with the passage of time.
In project work, estimates times should be obtained from managers or senior individuals who will be responsible for the project tasks later. Non-project staff often needs help when estimating tasks.
Estimates for Materials and Equipment Costs
Materials generally need two types of costing:
- the total expected costs including the charges and taxes payable for transportation
- the total lead-time, which is the time expected toe laps between issuing a purchase order and receiving the consignment.
If no provisional bills of materials yet exists it is good practice to work with engineers to prepare provisional bills of materials. Often, the engineers have a very good idea of the more significant and more expensive items. record of past projects can be consulted to help. The purchasing department should also be involved to prepare detailed estimates. This is to ensure the raw materials are obtained from the right supplier and at the correct price. Often, they can play a leading role in cost estimates. We must remember, however, that any taxes, shipping taxes, packing, insurance, port duties are taken into consideration. We also should use the validity of quotations sent from suppliers.
Reviewing cost estimates
We should be now able to produce bottom-up estimate. It is desirable also to take a wider look. A top-down estimate may be made for comparison. This often discovers other issues, that might not be previously taken into consideration. For example errors, corrections, modifications, writing reports etc. It is also important to prepare the costs to be authorised and signed off.
Sometimes, even after a sign off the clients idea of project scope might, change. Sometimes, technical staff comes up with new solutions. Therefore, at times, there might be different versions of project proposal and costs. Even when the plan is already agreed, schedules and cost estimates might need to change. Therefore, it is important to record all the findings and keep track of project versions continuously and up to date. Version control is important in project management.
Planning the Timescale
In the very early days of most projects there is no or little detailed information available about the project tasks. Anyone planning a project of significant size find that there is a number of internal and external factors that impact the project.

Generally, external factors will lie out of the control of project manager. They can also significantly affect the project planning and schedule. All projects are prone to risks, for example Acts of God. For example, earthquakes, hurricane, pandemic, lightning struck etc.
The actions of national governments - Fiscal policy - can also affect the project schedule. Governments funded projects might be abandoned due to change in policy. Grands and concessions might be changed.
Additionally, Corporate Strategy might change too. Decisions might be made to delay the projects by senior management, for example. Decisions might be made to change the project staff. Company might be taken over by another company.
Legislation and government policy might also impact the project. If project is carried out in different countries, the project manager would have to research local employment law, welfare, technical regulations before committing any resources to plan.
If figure above, we can also determine Working Factors which might affect the project plan. These are the day to day activities. They can apply to all sorts of projects and around different factors. For example, technical capabilities, attitudes and culture, capacity and availability of resources, supporting services, organisational structure, internal communications, systems and procedures or skills and competences. They can have a profound effect on the project outcomes. Project managers must learn these factors and plan according to the power and influence they can command.
The project, however, should promote efficient working. A well planned project stand greater change of success.
Bottom-up (task-led) planning
These are plans built on well defined tasks and estimates. Plans are made with careful consideration for resources availability, capabilities and performance. Bottom-up planning, has its dangers as it does not account for external factors that might influence the schedule.
Top-down (target led) planning
If a plan has target delivery requirements, all the tasks must be fitted in the available timeframe. One temptation here that must be strongly resisted by the project manager is to allow tasks durations estimates to be shortened only to meet the deadlines. Another danger is of removing all possible reserves. For example, planning to work constant overtime, so that the plan is too tight, leaving no time for error. Reducing time should never be done without any justification. Too optimistic times might satisfy senior management when the plan is submitted, but cause issues, conflicts and grief later on. Generally IT projects are target led. Relaxed scheduled, however, allow for breathing space, but danger of becoming slack should also be considered.
A project plan, must be presented in a way that communicates planned intentions to everyone. It should be visually effective and capable to convert by computer to useful reports. It should also include every significant project task. It should also determine completion timescale, from start to final closedown. Any waiting periods must be planned and indicated. for example waiting for a contractor to prepare a report, or manager to review data. The plan must be logical and tasks should be scheduled in a practical sequence. Estimates for planned tasks must be reasonable, constraints between tasks determined and the project should determine ket tasks and milestones. Priorities should be quantified and set the way to allow monitoring and project control.
The plan should be in a form, that can be processed by a computer to calculate produced project schedules, sorted into useful data order, flexible to change.
Comments