Project cost estimating
- Agnes Sopel
- Apr 10, 2022
- 9 min read

The most obvious reason for producing cost estimates is to assist in pricing decisions. We always need to be clear what costs we are talking about.
Some cost terms are important and we will mention them now to ensure it is all understood.
Cost escalation is the increase in any element of project cost where the cost of that element is compared between two different dates. It is usually expressed in a annual rate percent.
Direct costs can be attributed directly to the job. Materials, components, expenses and direct labour costs would be included to this category.
Factory cost is the total cost of a job or project before the addition of markup for profit. It compromises all direct and indirect costs of labour, material or expenses.
Fixed costs are when they are virtually unchanged. These typically include management and administrative salaries, rent, business rates, heating, insurance, building, maintenance and so on.
Figure below presents a simple cost a price structure for a manufacturing project.

Indirect costs are those costs which generally cannot be allocated directly to one job or project. The are often called "overhead costs" or "overheads".
Sometimes the classification of direct and indirect costs in an organisation can vary from project to project in organisations. This will depend on what customer agreed to pay. Cost estimators, must be clear on what contributes to project costs, both direct and indirect.
Whatever the industry, management always wants to keep the expenses as low as possible. The variable overheads costs however, its where the savings can be made the easiest way.
Labour burden is a percentage of wages added for various additional expenses. These can include paid holidays, illness or other absence, employee benefits, NI, etc.
Materials burden are the various costs added to a material cost. For example, administrative costs added to a shipment. A common rate is 15%.
Overhead recovery - most project costing systems adopt charging direct labour costs (including labour burden) as time recorded on the job, multiplied by a standard hourly cost applicable to the grade. An amount can be then added to this cost to recover indirect costs (overheads). The example in figure above presents this principle - 130% is normally applied over all similar projects carried out by a company. In some industries the overhead rate goes up to 200% or even higher. In labour intensive companies the overhead rate might be as much as 50%. Companies who keep their overhead costs low will keep the competitive advantage. Setting the percentage of overhead rates is an accounting task.
If the planned direct workload should fail, perhaps through cancelled order or over-optimistic sales forecast, the amount of direct labour costs that can be allocated to jobs and charged out in invoices will be less than the forecast. Because overheads are estimated as fixed percentage of the direct labour costs, the amount of revenue received to pay for overheads will also fall below the plan. The remedies can include:
- increase sales revenue by putting up the overhead rate through increased prices
- increase sales revenue by marketing drive to sell more products
- persuade some clients to agree to pay for previously indirect costs i.e drawings, telephone costs and other documents
- make economies to reduce the overhead costs.
If the overhead rate is too high, it might bring benefits in a short time, but longer term might not be competitive.
Prime costs is the sum of all direct costs needed to fulfil particular job or project. It is the direct labour + direct materials + direct expenses.
Standard costing is a system in which cost estimates and budgets are composed using standard costs from labour and materials. In projects these are used in cost estimating and job cost collection. By comparing the two if the same standard rates are used the performance can be measured. When the variances become significant, these must be reviewed and corrected as necessary.
Standard labour costs allow to classify people according to some convenient rules. This is usually based on the combination of the work and the salary structure.
Below figure is an example of such grades.

The number of standard grades should be kept to minimum. The accountant should use the standard salary costs for those in each grade. All the estimates and actual costs are using these grades. This also keeps it confidential.
Standard materials costs can be derived from commonly stocked materials and purchased components. These are calculated as averages based on unit costs in suppliers invoices.
Variable costs depend on the work activity. They are typically confined to direct costs, but may have indirect content.
Variance is any measured deviation between planned and budgeted quantity and the quantity actually used on the project. They define the cost differences. In project management they highlight errors, including errors with grades made by accountants.
Estimating accuracy

The more precise a project is defined the less estimating errors. Estimates always involve an element of personal judgement. The outcome can never be foretold with certainty. We should always, however, try to gather the data and make estimates to be as accurate as possible.
Often industries apply different levels of confidence to cost estimates.
Ballpark estimates - made before project starts. These are vague estimates when the work has not yet been decided. These are used to make preliminary checks to possible resource requirements. Generally expected at +/- 25% of confidence.
Comparative estimates - made by comparing work to a similar project. These are commonly used for tenders in manufacturing requirements. It is important to have, however, a level of confidence in the previous data. Generally expected at approx. +/- 15% of confidence.
Feasibility estimates - these are generated after a significant amount of project design has been established. Quotations are obtained from suppliers and material schedules are available. Generally expected at approx. +/- 10% confidence.
Definitive estimates - these are generally done when significant purchase orders have been made. These generally derive after comparative and feasibility estimates are done as part of routine review. The confidence should be at approx. 5% or better.
Bottom-up estimating
Reliable estimates are valuable assets for managers. The vulnerability of profits when costs exceed budgets are not appreciated. Planned profits may fall victims to many risks. Very often a comprehensive WBS can help with avoiding overruns of budget. A good coding system should also be designed to help budgeting and cost control. Generally top-down estimating structures can be helpful, but it is still necessary to check the bottom-up estimates for accuracy.
The first step in bottom-up estimating would be to compile the list of all project tasks. Preparation of a WBS and coding coding system should also reduce the risk of errors. It meed to be known, however that WBS describe a project in broader terms. Checklists, might be helpful for more accurate cost estimates. Many companies use them successfully.
We should compile as detailed task list as possible including anything that might cost money. Each task should be selected so that it is small enough to be visualised easily for estimating purposes. The tasks should also be large enough to describe a significant part of the whole project. Careful identification of significant tasks will allow for successful budgeting and estimates.
Once the task list has been completed the estimates of costs should be presented in as simple format as possible. Often companies develop procedures for project cost estimating. Accurate collection of data in a business can also be helpful. Observance of company policy on cost rates and costing methods ensures that these can be set in most logical manner that works for the business. The cost than can be added to each individual task.
Below a simple format to indicate project price.

Manufacturing costs
Estimates can also be made from drawings, specially in production environments. A set of manufacturing drawings is needed first. Every step of production or operation turning raw material to finished product can be listed in great detail and chronological order. Past data can help with the estimates of labour time in each production step. Tables of standard times in each production step might also be available. In some cases, the level of detail is very comprehensive. This should allow to make a very good estimates. Bills of materials and lists of components can be very useful. This all is to reduce errors and guesswork. Reliance on personal judgement should be made only if thee is a significant amount of experience and scientific measurement involved.
If the product drawings are not available estimating costs might become rather complex. However a good description of the product or service would be a good start. The design engineers may provide this information. Once the description is available some historic data of previous costings might be available. Some useful comparisons can be made to previous jobs. These should also be derived from the technical engineers. Further the production manager can make estimates of the work required to make the product in man-hours. Man-weeks or man-hours are generally chosen here. Once these have been established, the equipment hours can be calculated.
Estimates for labour times
Estimates of project labour times should be obtained from managers or senior individuals of the departments responsible for carrying out the work. Any departmental estimates should be reasonable and achievable. One master of estimating forms could be designed and sent to departments who can enter the estimates. These form is then passed to the next department until it is fully completed. Estimating is often regarded as an unpleasant task, therefore more direct approach is sometimes needed when collecting the data.
Sometimes it can be possible to ask for estimates during the network planning sessions. We must remember, however, that network estimates are only preliminary task descriptions and might not reflect more detailed descriptions and items emerging during further project planning stages. Material costs are not usually considered during the network planning sessions and, in most cases, separate meetings need to be held.
Personal canvasing might be, therefore, the best option. It starts from preparing a set of estimating sheets with task list and codes. The project manager can embark on a tour to all managers in logical order (according to WBS). It allows for enough attention in each department. Any estimate which appears unrealistic can be questioned on a spot. Some managers will need help in the project estimating task.
An estimating format for most general purposes is presented below.
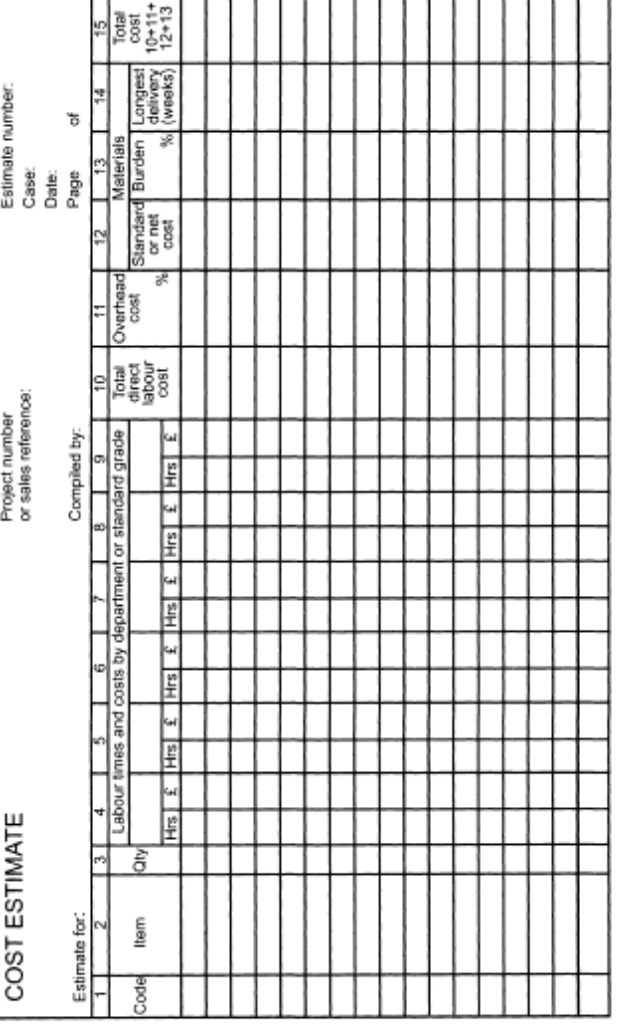
For large construction projects estimates format is available in below figure.
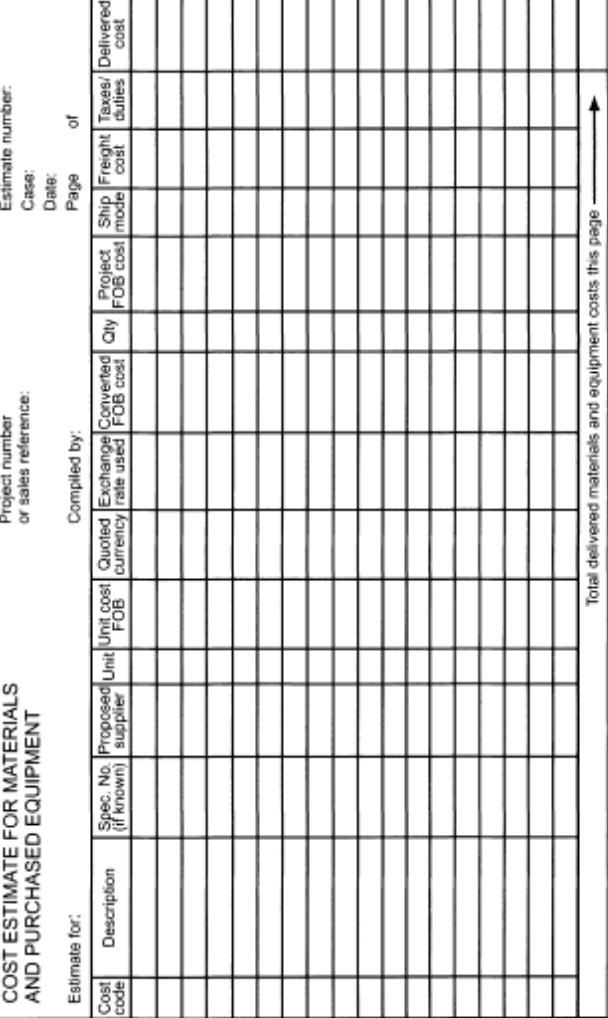
We must remember, however, that there are different types of estimators. Project cost estimating is never an exact science. Much of it might rely on subjective judgements. Some people always estimate on low side, others at high. There are optimistic estimators who always have high hopes for the job at hand. Most over, they barely learn from their experience. A good multiplication factor for such individuals would be approx. 1,5. In order words, add another 50% of time needed.
Occasionally, we might come across rather pessimistic estimators. They tend to overestimate most tasks. This will happen when they lack experience or confidence. However, higher estimates cause larger budgets. These 'empire builders' can often cause loss of tender or quotation.
Incompetence and inexperience can often be a causing factor to bad estimating. The project manager should be acceptable of such situations and instead of getting frustrated, make allowances and deal with the situation to the best of their ability.
Materials and equipment costs

When estimating the materials and equipment costs we need to take into consideration the relevant taxes, delivery charges and the lead time. At times, we might need to consider storage allowances and space. Past lists, bills of materials might be available to help this process. If drawings or bills of materials do not yet exist, the design engineers might be able to prepare provisional list of materials required. They often have a good idea of significant and expensive items required. This can improve the forecasting accuracy. The purchasing department should also be involved to ensure items will be obtained from correct suppliers at the correct cost and lead time. Additionally, cost of packing, delivery, insurance and other supplier costs should be included.
We must, however, always add allowances for contingency. For simpler projects 5% might be adequate, but higher risks might need more contingency allowances made.
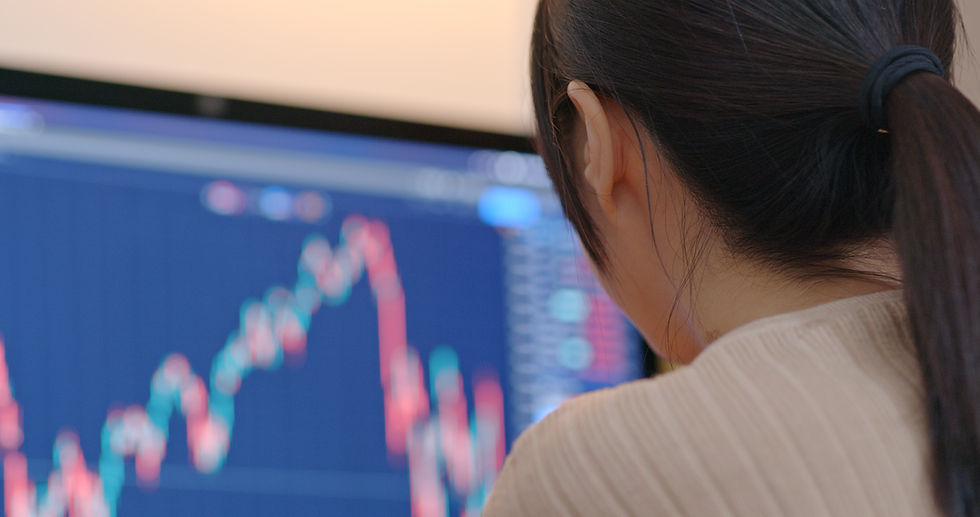
Inflation in estimating should also be considered. In countries where inflations are high, estimates might be an issue for a longer term projects. Inflation is, however, not easy to predict. These highly depend on economical, political and environmental factors. The rates might need to be negotiated with customers and contingency allowances included into contracts. The conditions of a contract might allow price increase in an event of cost escalation that is beyond the contractor's control.
Raise to uncertainly also can evolve around foreign currencies. Quotations in home currency might be the answer to mitigate these risks. It is common to calculate costs in one currency and then in convert to customer's own currency.
Reviewing the estimates
Once all information has been gathered it should be possible to prepare a comprehensive list of all costs. It is always a good idea to review the information. Any serious error could cause disastrous consequences. The estimates should always be checked as far as possible. These estimates will be used for many commercial and managerial decisions. It would be reasonable, also, to have them signed off, checked and approved.
Comentarios