Navigating Excellence: The Significance of Measuring Process Capability
- Agnes Sopel
- Aug 26, 2023
- 4 min read
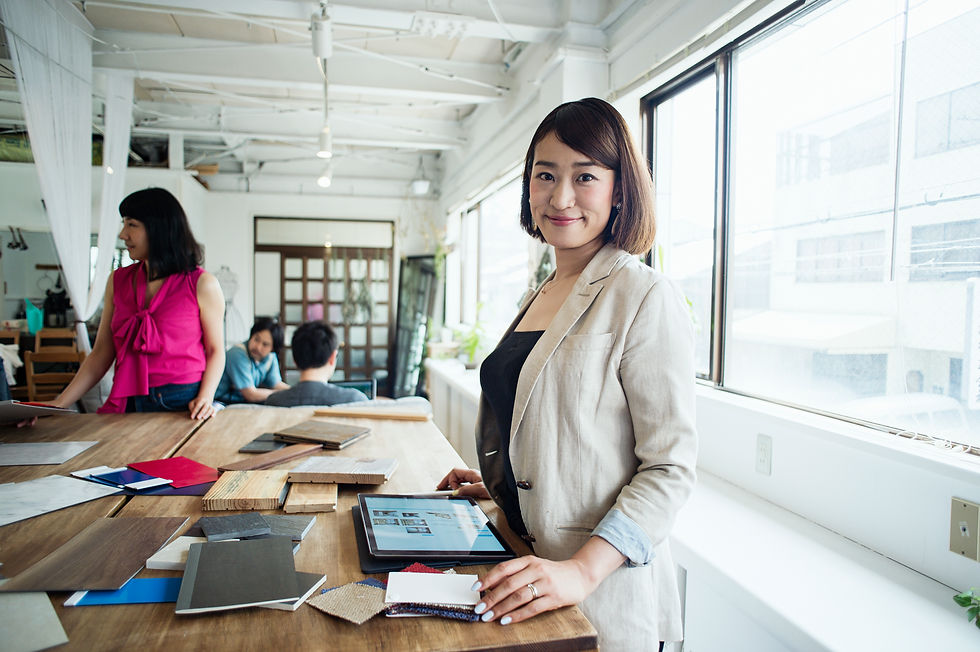
Introduction
In the relentless pursuit of excellence, understanding and measuring your process capability becomes the compass that guides your journey. It's the tool that empowers you to not only assess your performance but also make informed decisions for improvement. From defining critical parameters to unleashing the potential of Six Sigma, this article delves into the importance of measuring process capability and how it fuels your path to success.
Importance of Measuring Process Capability
Process capability is the measure of how well a process can produce products or services that meet customer specifications. Its significance lies in its ability to:
Ensure Consistency: Measuring capability reveals how consistently your process meets specifications, reducing defects and inconsistencies.
Drive Improvement: By identifying areas of deviation, you can strategise for targeted improvements that lead to enhanced quality and efficiency.
Customer Satisfaction: Capability measurement directly impacts customer satisfaction, as products that meet specifications enhance trust and loyalty.
Approaches for Continuous and Discrete Data
Continuous Data: For continuous data that follows a normal distribution, process capability is often assessed using indices such as Cp, Cpk, Pp, and Ppk.
USL and LSL: These are the Upper Specification Limit and Lower Specification Limit, representing the acceptable range of values set by customer requirements.
Process Capability Index: Cp and Cpk quantify how well the process spread fits within the specification limits.
Process Capability Target: This represents the desired value within the specification limits where the process should ideally operate.
Non-Normal Data: For data not following a standard normal distribution, alternative methods like Z-score transformations can be used to calculate process capability and performance. Z-score allows comparisons across different types of data.
Calculating Defects and DPMO
DPMO (Defects Per Million Opportunities): It calculates the rate of defects in a process, a crucial metric in assessing performance.
DPO (Defects Per Opportunity): Focuses on defects in individual units or opportunities.
DPU (Defects Per Unit): Counts defects within each unit.


Process Improvement in Manufacturing
Consider a manufacturing environment with customer complaints and return rates. By analysing the data, calculating DPMO, and employing Six Sigma principles, you can drastically reduce defects, improve customer satisfaction, and boost operational efficiency.
Z-score acts as a universal translator, allowing you to compare different processes and their capability levels. The goal is to achieve a Six Sigma process (1.5 DPMO), minimising defects and elevating performance.
Imagine a process initially operating at 3 sigma (66,807 DPMO). Through rigorous analysis, root cause identification, and targeted process improvements, you can systematically bring down defects to achieve a 6 sigma level (3.4 DPMO).
Process shifts can impact both short-term and long-term capability. Understanding this difference is key to addressing deviations and maintaining consistent performance.
The % Yield table acts as a compass, connecting process capability to sigma values. It quantifies the relationship between defects and the level of process excellence achieved.
Example: Calculating Z-score
Let's walk through an example of calculating the Z-score using Excel. The Z-score is used to determine how many standard deviations a data point is away from the mean of a distribution. Here's a step-by-step guide with detailed explanations and calculations:
Suppose we have a dataset of test scores from a class, and we want to calculate the Z-score for a specific student's test score.
Data Setup: Let's assume the following test scores for a class: 85, 78, 92, 88, 95, 72, 98, 90, 82, 87. We'll calculate the Z-score for a student who scored 88.
Calculate Mean and Standard Deviation: In Excel, use the AVERAGE function to calculate the mean and the STDEV.P function to calculate the population standard deviation. Mean: =AVERAGE(A1:A10) (assuming the data is in cells A1 to A10) Standard Deviation: =STDEV.P(A1:A10) Suppose the mean is 87.7 and the standard deviation is 7.72.
Calculate Z-Score: The Z-score formula is: Z = (X - μ) / σ, where X is the data point, μ is the mean, and σ is the standard deviation. Z-Score: =(88 - 87.7) / 7.72 Calculating this, we get a Z-score of approximately 0.0389.
Interpreting the Z-Score: A positive Z-score indicates that the data point is above the mean, while a negative Z-score indicates it's below the mean. In this case, our Z-score is positive (0.0389), indicating that the student's test score is about 0.0389 standard deviations above the mean.
Using Excel to Calculate Z-Score: You can directly use the formula to calculate the Z-score in Excel. In a cell, enter the formula =(X - μ) / σ, where X is the specific data point, μ is the mean, and σ is the standard deviation. For our example: =(88 - 87.7) / 7.72 The result will be the Z-score for the given data point.
Let's consider an example of calculating the Z-score for customer complaints in a manufacturing setting.
Suppose you work for a manufacturing company that produces electronic devices. You're analysing customer complaints related to defects in these devices. You want to calculate the Z-score for the number of defects reported for a particular model.
Data Setup: Let's assume you have data for the number of defects reported for a specific model of electronic devices over a period of time: 4, 6, 8, 5, 7, 3, 9, 6, 5, 7. You want to calculate the Z-score for the number of defects reported, assuming the population mean and standard deviation for this model are 6.5 and 2.3, respectively.
Calculate Z-Score: The Z-score formula is: Z = (X - μ) / σ, where X is the data point (number of defects), μ is the mean, and σ is the standard deviation. Let's say you're calculating the Z-score for a reported number of defects of 7. Z-Score: =(7 - 6.5) / 2.3 Calculating this, you get a Z-score of approximately 0.2174.
Interpreting the Z-Score: A positive Z-score means the reported number of defects is above the mean, while a negative Z-score means it's below the mean. In this case, the Z-score is positive (0.2174), indicating that the reported number of defects for this specific model is about 0.2174 standard deviations above the mean.
Using Excel to Calculate Z-Score: You can easily calculate the Z-score in Excel. In a cell, you can enter the formula =(X - μ) / σ, where X is the reported number of defects, μ is the mean, and σ is the standard deviation. For our example: =(7 - 6.5) / 2.3 The result will be the Z-score for the reported number of defects.
Conclusion: A Journey to Excellence
Measuring process capability is not just a metric; it's a transformative journey that empowers you to navigate towards excellence. Armed with the tools to analyze, improve, and elevate performance, you can steer your organization through the seas of challenges and towards the shores of success. So, set sail on this voyage, armed with the knowledge to chart your course and create a legacy of process excellence.
コメント