Mastering 5S+ Implementation: Tips for ISO Consultants
- Agnes Sopel
- Sep 18, 2023
- 5 min read
Are you an ISO consultant looking to optimize your clients' operations and streamline their processes? If so, then understanding and effectively implementing the 5S methodology can be a game-changer. In this blog, we'll explore essential tips for ISO consultants and introduce a valuable tool—the 5S Gap Analysis Table—to help you navigate the world of 5S implementation.
Understanding the 5S Methodology
Before diving into the tips, let's briefly review what the 5S methodology is all about:
5S stands for:
Sort: Remove unnecessary items from the workspace.
Set in order: Organize and arrange necessary items for efficiency.
Shine: Clean and maintain the workspace regularly.
Standardize: Establish and adhere to standardized processes.
Sustain: Ensure the continued adherence to the 5S principles through training and culture building.
5S is a lean management tool originating from Japan, primarily associated with manufacturing. However, its principles can be applied across various industries to enhance productivity, reduce waste, and create a safer and more efficient work environment.
Now, let's delve into the tips for ISO consultants to master 5S implementation:
1. Emphasize a Holistic Approach
The research findings suggest that successful 5S implementation in Japanese organizations is based on a holistic perspective. ISO consultants should encourage clients to adopt this mindset, focusing not only on workspace organization but also on how 5S can influence overall organizational and management decision-making.
2. Visual Methods Matter
Visual methods, as highlighted in the research, play a crucial role in 5S success. Encourage clients to use visual cues, such as charts, diagrams, and models, to communicate and reinforce 5S principles. The me-de-miru approach can make it easier for employees to understand and adhere to 5S practices.
3. Assess Maturity Level
Understanding where your clients stand in their 5S journey is essential. The research suggests that service organizations may be in the earlier stages of 5S development compared to manufacturing companies. Tailor your approach based on their maturity level and offer guidance accordingly.
4. Tailor Terminology and Approach
Recognize that 5S terminology and management approaches may differ between cultures. The study found that Japanese 5S practices use different terms and emphasize holistic management. ISO consultants should adapt their language and strategies to align with the client's cultural context.
5. Promote Total Participation
Total participation is a cornerstone of Japanese 5S practices. Encourage your clients to involve all levels of their organization in 5S planning and implementation. Emphasize that participation should extend beyond the shop floor and encompass strategic decision-making.
6. Understand Autonomy
In Japanese 5S, autonomy is highly valued. Help your clients understand that granting autonomy can enhance 5S implementation. Employees who have a sense of ownership are more likely to contribute effectively to the 5S process.
7. Implement Visual Methods (me-de-miru)
Visual methods, including photos, diagrams, and charts, can be success factors for 5S implementation. Help your clients incorporate these tools into their 5S strategy for better communication and understanding.
8. Use the 5S+ Gap Analysis Table
One valuable tool for ISO consultants is the 5S Gap Analysis Table. This table helps you assess the current state of 5S implementation and identify areas for improvement. Here's a simplified version of the table:
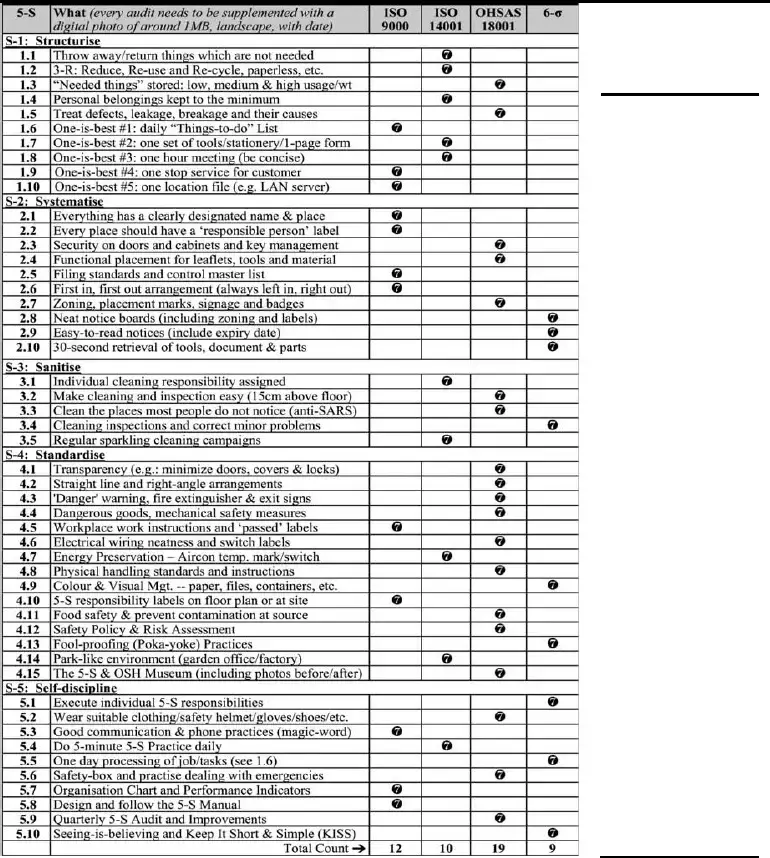

Use this table to collaboratively evaluate the client's 5S practices in each category. Assess what's currently in place, define the desired state, and identify the gap. This structured approach can guide your consulting efforts and provide a clear roadmap for improvements.
In the world of modern management, where efficiency, quality, and sustainability are paramount, tools that can streamline processes and integrate various management systems are highly valuable. This is where the 5S+ Gap Analysis Audit Checklist comes into play. This tool, introduced and refined by experts in the field of Total Quality Management (TQM), offers a structured approach to enhancing organization-wide efficiency and effectiveness. In this article, we will explore how to use this checklist effectively and the benefits it can bring to your organization.
Understanding the 5S+ Gap Analysis Audit Checklist
Before we dive into how to use the 5S+ Gap Analysis Audit Checklist, let's clarify what it entails:
5-S and L5S: The 5S methodology, also known as 5-S, stands for Sort, Set in Order, Shine, Standardize, and Sustain. It's a lean management tool originating from Japan. L5S, or Lean 5S, is an advanced version of 5S that focuses on minimizing wastage.
Integration of Management Systems: The checklist aims to integrate multiple management systems, including ISO 9000 (Quality), ISO 14001 (Environmental), OHSAS 18001 (Occupational Health and Safety), and Six Sigma (a quality improvement methodology).
Audit Process: The checklist serves as a tool for auditing an organization's practices in these areas. It helps identify deficiencies and opportunities for improvement.
Using the 5S+ Gap Analysis Audit Checklist
Now, let's discuss how to use the 5S+ Gap Analysis Audit Checklist effectively:
Step 1: Preparation
Ensure you have access to the 5S+ Gap Analysis Audit Checklist. You can customize it to suit your organization's specific needs.
Step 2: Audit Team
Assemble a team of auditors who are knowledgeable about the organization's operations and familiar with 5S and related management systems.
Step 3: Clear Objectives
Define the objectives of the audit. Are you assessing compliance with standards, identifying areas for improvement, or measuring progress? Having clear objectives will guide the audit process.
Step 4: Conduct the Audit
Perform the audit, focusing on each of the components: 5S, ISO 9000, ISO 14001, OHSAS 18001, and Six Sigma. Evaluate the organization's practices in each area.
Step 5: Document Findings
Use the checklist to document your observations. Note what is currently in place and what needs improvement. Identify deficiencies (Non-Conformances or NCs) and observations (OBs).
Step 6: Analyze Results
Compile the findings for each component. Analyze the gaps between the current state and desired state in each area.
Step 7: Create an Action Plan
Develop an action plan based on the identified gaps. Outline specific steps, responsibilities, and timelines for addressing deficiencies.
Step 8: Monitor Progress
Implement the action plan and regularly monitor progress. Use the 5S+ Gap Analysis Audit Checklist periodically to track improvements.
Step 9: Foster Integration
Encourage integration among the different management systems. Show how improvements in one area can benefit others, emphasizing a holistic approach to management.
Benefits of the 5S+ Gap Analysis Audit Checklist
Integration: The checklist promotes the integration of various management systems, ensuring they work in harmony towards common objectives.
Efficiency: By identifying deficiencies and streamlining processes, organizations can become more efficient, reducing waste and saving resources.
Quality: Enhanced quality practices, compliance with standards, and continuous improvement lead to higher product and service quality.
Sustainability: The checklist emphasizes environmental and safety considerations, contributing to sustainable and responsible business practices.
Competitiveness: A well-integrated management system can give organizations a competitive edge, especially in today's global marketplace.
In conclusion, the 5S+ Gap Analysis Audit Checklist is a powerful tool for organizations striving for excellence, efficiency, and sustainability. By using this tool, you can assess, integrate, and continuously improve your management systems, ultimately driving the success and competitiveness of your organization. It's not just a checklist; it's a roadmap to excellence.
Conclusion
As an ISO consultant, your role is to guide organizations towards greater efficiency and excellence. By mastering the 5S methodology and implementing these tips, you can help your clients create a workplace that's not only well-organized but also strategically aligned with their goals. Remember, 5S is more than just a set of tools; it's a holistic approach to management and continuous improvement. Use the 5S Gap Analysis Table to assess, plan, and monitor progress as you lead your clients on their 5S journey.
Comments